Plastic extrusion services for custom industrial applications
Plastic extrusion services for custom industrial applications
Blog Article
A Comprehensive Guide to the Refine and Benefits of Plastic Extrusion
In the vast realm of production, plastic extrusion arises as a important and highly effective process. Transmuting raw plastic right into constant accounts, it accommodates a myriad of industries with its impressive adaptability. This guide aims to clarify the complex steps associated with this method, the kinds of plastic proper for extrusion, and the game-changing benefits it gives the market. The taking place conversation assures to unravel the real-world effects of this transformative procedure.
Comprehending the Basics of Plastic Extrusion
While it may appear complex at first look, the procedure of plastic extrusion is basically basic. The procedure starts with the feeding of plastic material, in the type of granules, powders, or pellets, into a warmed barrel. The shaped plastic is after that cooled down, strengthened, and cut right into desired sizes, completing the procedure.
The Technical Refine of Plastic Extrusion Explained
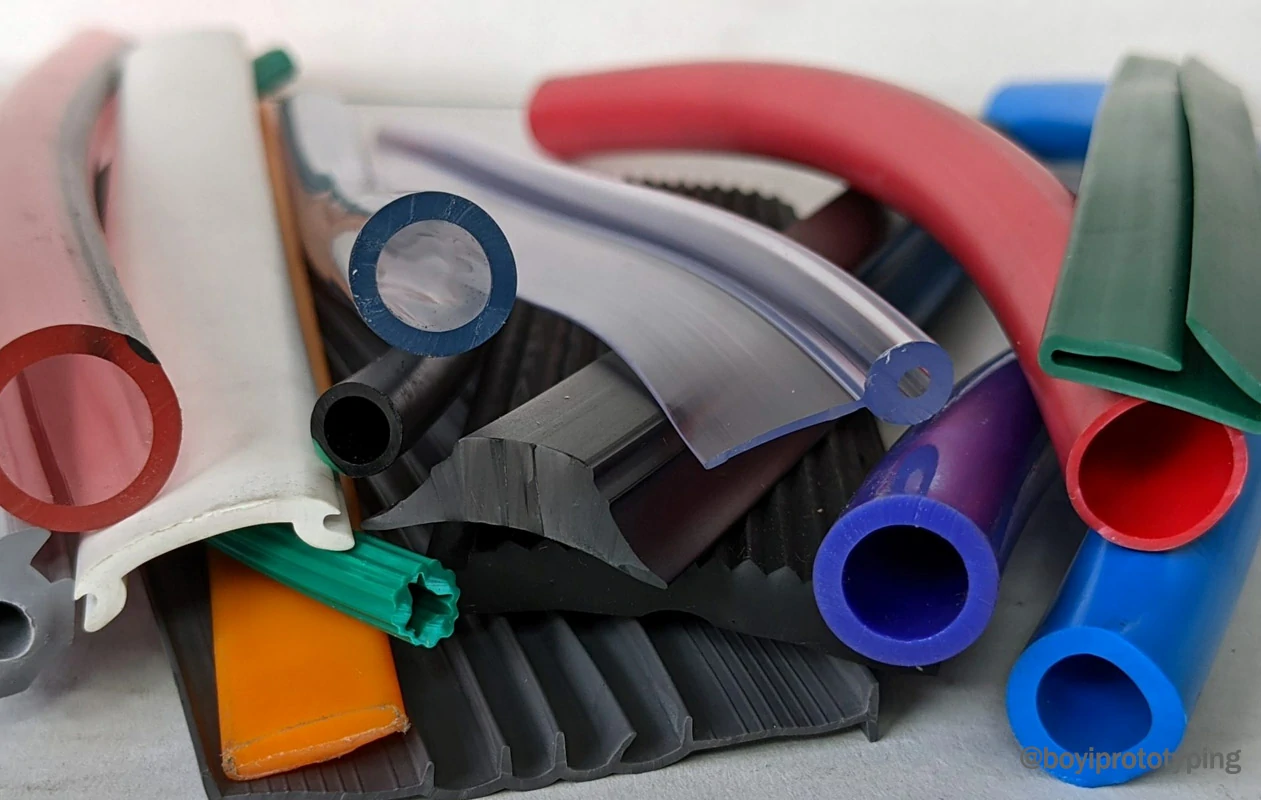
Kinds Of Plastic Suitable for Extrusion
The choice of the ideal kind of plastic is an important aspect of the extrusion process. Different plastics use distinct properties, making them extra fit to certain applications. Recognizing these plastic kinds can dramatically enhance the extrusion process.
Comparing Plastic Extrusion to Various Other Plastic Forming Techniques
Understanding the sorts of plastic appropriate for extrusion leads the way for a wider conversation on just how plastic extrusion compares to other plastic forming techniques. These include shot molding, strike molding, and thermoforming. Each approach has its special uses and benefits. Injection molding, for example, is exceptional for creating detailed components, while impact molding is perfect for hollow objects like bottles. Thermoforming excels at creating shallow or huge parts. Plastic extrusion is unrivaled when it comes to creating continual profiles, such as gaskets, seals, and pipes. It navigate to these guys additionally enables a consistent cross-section along the length of the product. Hence, the selection of technique mostly relies on the end-product requirements and specs.
Key Advantages of Plastic Extrusion in Manufacturing
In the realm of production, plastic extrusion offers many considerable advantages. One notable benefit is the cost-effectiveness of the procedure, that makes it a financially enticing manufacturing approach. Furthermore, this technique offers superior item flexibility and boosted production speed, therefore raising overall manufacturing efficiency.
Affordable Manufacturing Method
Plastic extrusion jumps to the forefront as an economical production technique in production. This process attracts attention for its capacity to create high volumes of material swiftly and efficiently, offering manufacturers with substantial cost savings. The primary cost benefit is the capacity to make use of cheaper resources. Extrusion makes use of polycarbonate products, which are less pricey compared to ceramics or steels. Even more, the extrusion process itself is fairly basic, minimizing labor prices. In addition, plastic extrusion calls for less power than typical production approaches, adding to reduced functional expenses. The process additionally minimizes waste, as any type basics of defective or excess products can be recycled and reused, giving one more layer of cost-effectiveness. Generally, the economic advantages make plastic extrusion a highly appealing choice in the manufacturing market.
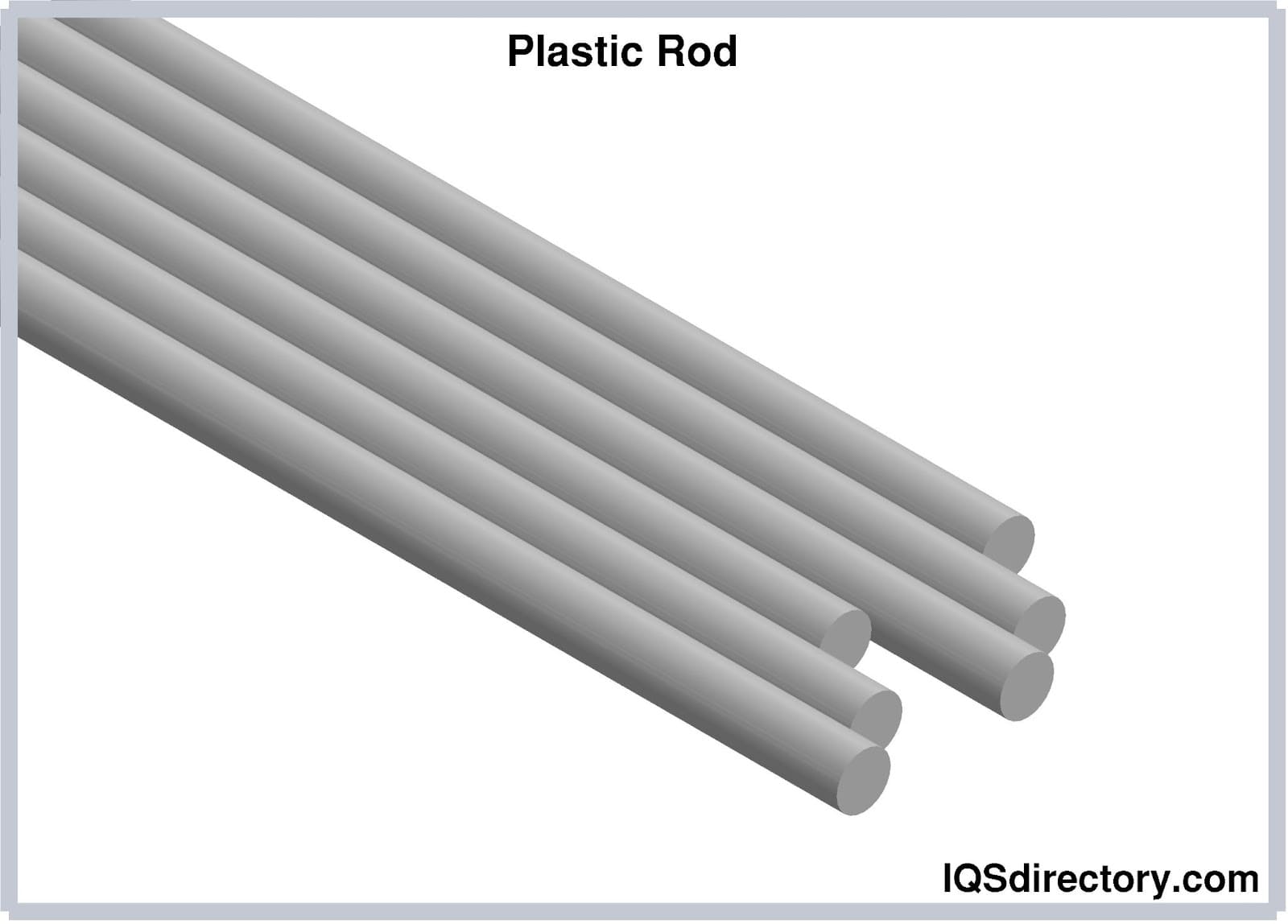
Superior Product Flexibility
Past the cost-effectiveness of plastic extrusion, another significant advantage in making lies in its exceptional item versatility. This makes plastic extrusion an ideal remedy for markets that require tailored plastic components, such as automotive, construction, and packaging. In essence, plastic extrusion's item versatility fosters technology while improving functional performance.
Boosted Manufacturing Rate
A substantial benefit of plastic extrusion lies in its improved manufacturing speed. Couple of various other production procedures can match the rate of plastic extrusion. Furthermore, the ability to maintain consistent high-speed manufacturing without compromising product top quality sets plastic extrusion apart from other methods.
Real-world Applications and Impacts of Plastic Extrusion
In the realm of manufacturing, the technique of plastic extrusion holds profound relevance. The economic advantage of plastic extrusion, primarily its affordable and high-volume output, has actually transformed manufacturing. The sector is persistently aiming for technologies in recyclable and naturally degradable materials, indicating a future where the benefits of plastic extrusion can be kept without endangering environmental sustainability.
Final thought
To conclude, plastic extrusion is a very reliable and efficient technique of transforming basic materials right into varied products. It offers many benefits over various other plastic forming techniques, including cost-effectiveness, high outcome, very little waste, and design versatility. Its effect is profoundly felt in different industries such as construction, find more information auto, and consumer goods, making it a pivotal procedure in today's production landscape.
Delving deeper into the technological procedure of plastic extrusion, it starts with the selection of the appropriate plastic material. When cooled down, the plastic is reduced into the required sizes or injury onto reels if the product is a plastic film or sheet - plastic extrusion. Contrasting Plastic Extrusion to Other Plastic Forming Techniques
Comprehending the kinds of plastic suitable for extrusion paves the way for a wider discussion on just how plastic extrusion piles up versus various other plastic forming techniques. Couple of various other manufacturing processes can match the rate of plastic extrusion.
Report this page